Taper
Lock is a complete system of tapered drills, tapered fasteners and tapered
gauges.
Taper Lock Fastener holes can be accomplished quickly with a
high degree of accuracy, confidence and security.
It is essential that the Taper Lock System be accompanied by
excellent craftsmanship. Regardless of the higher degree of accuracy,
engineering and quality, the ultimate result depends on who builds the product.
The
Taper Lock System has its own built-in quality controls. Reasonable care
installations will ensure proud finished products. By following this exceptional
system, each conscientious craftsman will receive great satisfaction knowing
that each Fastener has been installed accurately. The obvious results obtained
from excellence is gratification.
Taper Locks have changed the equations in structural life
computations. These Fasteners and Systems are composed of tapered conical shank
fasteners. Tapered precision holes, together with preloads and interference are
all uniformly controlled.
The advancement of the interference fit effectively impacts
preload. Radial compression, static preload and peripheral tension, effectively
reduce stress and proportionately improve fatigue life.
The high performance of Taper Lock Fasteners will continually
provide structural integrity in existing and future designed vehicles and
products.
The
term Taper Lock is derived from the fact that this tapered fastener is
self-locking.
When the tapered fastener is inserted into a correctly tapered hole, the
interference fit secures the fastener and locks it. This prohibits it from
turning, eliminating wrenches, other types of holding and special costly
operations.
Taper Lock Fasteners have accurately ground precision shanks
inserted with a mating precision tapered hole and a mating Washernut® assembly.
A washer and free turning nut make up the assembly that provides automatic
washer centering. The “Washer Nut” is extremely strong. The washer is
captured to the nut while allowing the nut to turn freely. These features
eliminate the loss of washers or handling inventory and installations. Fumbling
is eliminated.
Taper
Lock’s superiority is its controlled interference fit.
Preload is induced at the wall of the hole and progresses through the material,
diminishing to zero at some distance from the hole’s edge.
Regular Fasteners must be driven or pressed the full length
of the hole when attempting interference fits. This procedure forces the walls
outward, tending to promote seizure, galling, plating damage and broaching the
hole. The result is non-uniform preloading. This action creates areas of
concentrated and near zero stress. Thus the fastener purpose is defeated.
The Taper Lock Fastener fits freely into
the greatest portion of the hole and need travel only a short distance to become
full interference, uniformly preloading as the walls expand. This provides
longer wear and greater strength. This allows Taper Locks to be removed without
damage to the fastener or the hole.
Taper Lock’s superior joint
strength occurs through even load distribution and requires fewer fasteners.
Closer hole spacing than other conventional fasteners is allowed. Nut height is
reduced allowing greater wrenching freedom in inaccessible or tight places.
Two types of Taper Lock Fasteners exist—threaded and
non-threaded. All threaded fasteners use the mating Washernut®.
Taper Lock Fasteners are available in
grip lengths of 1/16 or 1/32 increments. Charts are provided by fastener
manufacturers for the ranges of thickness for each grip length.
The 100º Flush Head type fasteners are
measured from the top of the head to the end of the full conical portion of the
shank. The Protruding Head type fasteners are measured from under the head to
the end of the conical shank.
The Taper Lock Drilling System has
many qualified positive feed power and motor drilling units available.
Quackenbush provides In Line, Right Angle and Self Colleting tools. They compete
favorably for business with Cooper Tools, Rockwell, Buckeye, Gardner Denver,
Peck Drill, Doler, Dotco, Chicago Pneumatic and Winslow Spacematic products.

Quackenbush offers Q-Matic to Spacematic customers.
Quackenbush has gained fairly broad acceptance for use with drilling Taper Lock
holes. UNITED's Helox Shelox and Nurlock Adapter Systems complement
Quackenbush Positive Feed Motors. Helox Shelox assures the user drilling
accuracy and precision depth control with total SPC Gauging for Taper Lock
drilling and installation.
UNITED Taper Lock Tooling Components adapt to
Spacematic, Quackenbush, Chicago Pneumatic, Rockwell, Cooper, Keller, Buckeye,
Dotco, Doler, and Gardner Denver drill motors.
UNITED’s Helox®
Shelox® Depth Control and Sensor System
designed for space saving drilling on irregular or contoured surfaces. Helox®
Shelox® also adapts to these motors accurately guiding and directing cutters,
coolant and controls to assure safe, secure and accurate Taper Lock drilling and
fastener installation.
The Spacematic, a fast positive
feed motor, is air operated with depth control. It requires ample operating
room, but does not require pilot holes. Details are available in this section.

Chicago Pneumatic Power Motors are small air operated
units and have maximum capability of 3/16 group 3 Taper Lock holes. These units
can be used with UNITED’s Micro Controlled Countersink Super Stops,
also in this section. The Chicago Pneumatic Unit operates at 15000 r.p.m. Pilot
holes are required for reaming.
Buckeye Power Units are medium size and air operated.
Their units operate at 500 r.p.m. or more. Use UNITED’s Micro
Controlled Countersink Super Stop with Buckeye. They are shown in this section
Taper Lock Coolant and Cutting Fluids were explained by
P.F.S. Omark Applications Engineering Laboratory as follows:
“ALUMINUM cutting fluids for drilling and reaming
aluminum and other soft metals with high speed steel cutters are air, air and
water mist, soluble oil in either mist or flooding forms, refrigerated air,
liquefied Freon and light mixtures of mineral or lard oil. Soluble oil is most
poplar for a broad variety of applications when mixed in a ratio of 1:30 with
water. Liquefied Freon is to be used with great care in well ventilated
areas. This is due to high toxicity levels. Cetyl alcohol is suitable for hand
reaming.”
“TITANIUM and ALLOY STEEL Drilling and Reaming with
M33 or M42 Cobalt high speed cutting uses air, air and water mist or flooding
and liquefied Freon. Use liquefied Freon with great care and only in well
ventilated areas. Beware of its high toxicity levels. For heavy duty
drilling, sulphurized cutting oil containing only up to 2% active sulphur may be
successfully used.”
All types of Taper Lock Fasteners, with the exception of low
interference type, do not require wrenching, sockets or other holding tools.
All Taper Locks are installed into a tapered hole
simultaneously locking the fastener in the hole.
Seating the Taper Lock Threaded Fastener occurs through the
transfer of torque onto the mating nut. Taper Lock Collars are swaged sealed
with a rivet gun.
P.B. Fastener, Deutsch, SPS, Voi Shan and BlancAero all
provide full and complete Taper Lock techniques and details for their respective
fastener installation and removal.
UNITED’s commitment is to provide our industry Taper
Lock quality tooling in line with our goal —
FIRST - ON TIME - FASTER - LOWER COST!
Taper Lock Gauges are provided by UNITED
for checking hole diameters, countersinks, bearing, finish and depth.

The UTLG-5100-A and -B Gauge Assemblies check the hole
diameter at two points for 100º countersink holes. Sleeve and Pin check 'B'
charted diameter (lower check point) in the countersink hole. Reverse the
bushing sleeve and pin and check the upper 'B' diameter.
The UTLG-5120 Countersink Depth
Gauge checks the depth at countersink holes and is used in setting up all
drilling equipment to accurate depths.

Each Gauge is simple, accurate and a fast method of
inspecting Taper Lock holes.
One advantage of the Taper Lock System is that the fastener
itself acts as a gauge. Simply place this fastener in the hole by firm hand
pressure and measure the protrusion of the head above the material. Divide the
measurement by 48. The result is the exact interference between the fastener and
the hole. It is not possible to install the incorrect fastener in a Taper
Lock hole.
UNITED’s Taper
Lock Tooling System includes Air Motors, Depth Sensors, Drills, Drill Reamers,
Micro Stop Cages, Guide Bushings, Fastener Installation and Removal Devices and
all Product and Installation Gauges. UNITED conversion spindles
are available to adapt Spacematic, Q-matic and other air-powered tools to all UNITED
tooling.
Selecting the correct Drill,
Reamer, Countersink and hole sizes for Flush Head Fasteners or Protruding Head
holes requires simple efficient operations. Tapered tooling is provided
for every Taper Lock size fastener. The tapered tools are relieved on backout
which eliminates chip galling and adds accuracy and smooth hole finishes. The
famous Taper Lock Drill Reamer has cutting lips at the end of the tool and
reamer flutes on the sides.
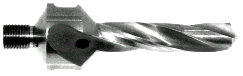
UNITED Taper Lock tools are manufactured to the highest
standards of quality, precision and accuracy with the longevity required to
complete your products on time the first time.
By using UNITED’s precision
tapered Depth Control and Gauge tooling, operator excellence can avoid these
common pitfalls:
A. Eccentricity from worn power tools, spindles or
countersink cages
B. Improper support of the power feed tools
C. Forced feeding and excessive tool pressure
D. Chip overload and galling
E. Improperly sized pilot holes
F. Incorrect tool feeds and speeds
G. Dull tools causing crooked starts
H. Improper drill alignment
I. Inaccurate power feed, speed or stop adjustments
J. Excessive dwell in the hole at the correct hole depth
causing poor finish and oversized holes.
UNITED recommends
these installation techniques:
A. Hold the workpieces together clamped securely in place.
B. Accurately drill pilot holes through precision Blocks and
Drill Bars.
C. Use correct Taper Drills, Drill Reamer Tools,
Countersinks, Super Stop Cages and accurate Depth Control Units.
D. Free the holes of chips and coolant before and after
reaming.
E. Press the fastener head down securely by hand after
placing in the hole.
F. Check the head protrusion with the UTLG-5130 Gauge before
installing the nut.
G. If head protrusion is accurate, install and tighten the
nut with a rivet gun and bar.
H. Seat the fastener using a rivet gun and bucking bar with a
hollow phenolic insert.
I. Place the aluminum swage collar over the fully seated
grooved fastener end.
J. Place the gun with a rivet set over the collar with a
bucking bar placed against the fastener head.
K. Apply rivet driving pressure and form the collar into the
grooved end of the fastener.
L. When the fastener is fully seated, trim off any excess
material.
M. The Taper Lock should now be fully swaged with a trimmed
collar and tightly seated head.
N. The protrusion of the Taper Lock’s fastener’s threaded
end must be within the specific protrusion limits.
The Taper Lock Fastener Removal Tool
provides an easy means of removing the fastener. If the collar is improperly
formed, cracked or loose, remove the fastener by first using a power tool with a
hollow mill cutter until the cutter is seated on the fastener’s end.

Remove the fastener with a sharp tap on UNITED’s
Taper Lock Knock Out Tool installed on the fastener’s threaded end without
damaging the thread. (Refer to Taper Lock Knock Out Tool UDB-710255 in this
section.) Clean the hole and reseat the fastener following UNITED’s installation
steps.
UNITED Micro
Super Stop Drill Cages have indexing graduations
which assure depth control within .001 inch. A Drill Bar Foot is provided which
is placed flush to the workpiece surface to guide this Micro Super Stop
precisely. This assures straight holes on size and normal to the workpiece.

When using UNITED’s Micro Controlled Countersink
Super Stop, be sure to keep the drill cage and drill bar perfectly flat
against the structure before reaming commences.
Hold the unit firmly but allow a light feed
pressure. Allowing your drill to dwell after the hole is completed will cause
oversized holes. Withdraw while the motor is running. Withdraw frequently to
remove chips. Abnormal cutting or wobbling will also cause oversized holes. When
hand reaming or drilling, the pressure is of great importance. Less pressure and
a “different feel” are required as compared to straight drilling. See
the following speed recommendations in the chart.